Crushing It
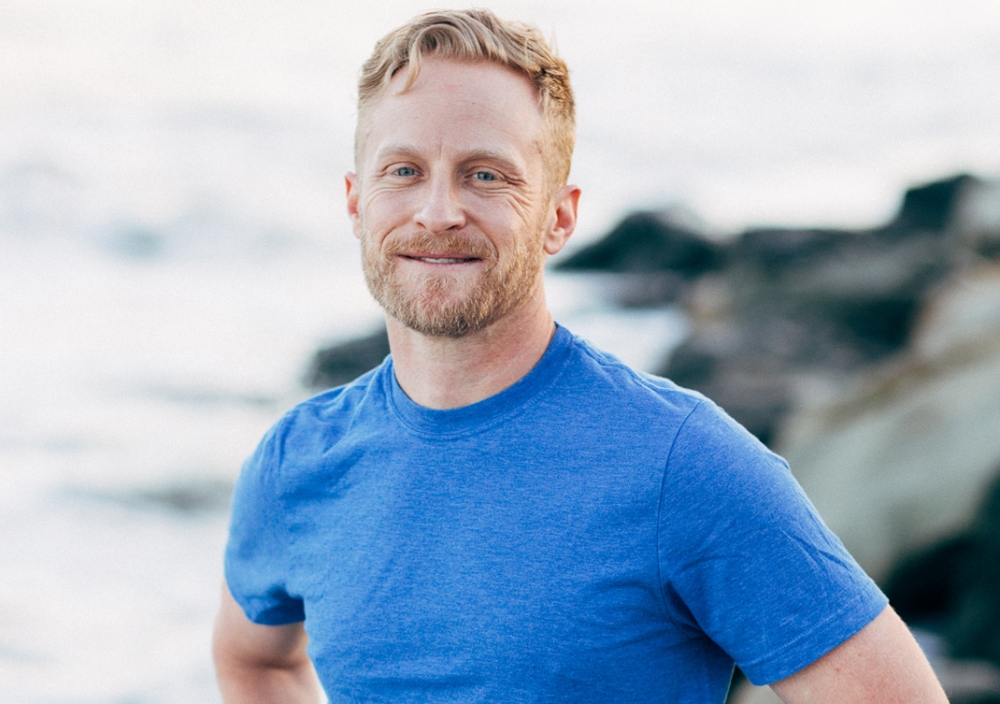
Question: When you’ve designed the world’s most efficient metamaterial, one that could change the way cars, planes and even space exploration vehicles are built, is mostly air yet reaches the theoretical bounds for stiffness and strength and can equally resist forces coming from any direction, what do you do next?
Answer: You break it.
At least, that’s what a team of materials scientists including Jonathan Berger of UC Santa Barbara and Jens Bauer of UC Irvine did. Their goal? To learn what boundaries could be pushed with a novel metamaterial called plate-nanolattice. The research findings are published in a paper in the journal Nature Communications.
“A metamaterial is an engineered material system that has properties — mechanical, electrical, thermal, or some combination thereof — that are beyond those available in nature,” Berger said “This obviously has the potential to be a broad category of materials, and is usually reserved for systems that are radically different from natural systems.”
For designers such as Berger, the search is on for combinations of architecture and constituent materials "to achieve systems with extreme lightweight stiffness and strength.”
Developed in 2015, Berger’s Isomax™ design, named for its property of maximal stiffness in all directions, is a foam consisting of ordered cells of superimposed hollow cubes, pyramids, and octahedrons. For its density, Isomax™ was predicted to be one of the stiffest metamaterial designs out there, due to its ability to resist shearing and crushing from any direction. This opens up new possibilities in the world of performance materials, where the rare combination of lightness and strength are highly sought.
The design caught the attention of Jens Bauer, who specializes in mechanical and aerospace engineering, and is the lead investigator in the Nature Communications study. In his line of work, strong, lightweight materials are particularly important; they could become part of the design for future cars, planes, and even space vehicles.
“The cubic+octet (Isomax™) topology is one of several designs that had been predicted to reach the theoretical performance limit for a porous material,” said Bauer. “While this was all theory, our goal was to actually make a material that reaches that limit and to finally prove those predictions which go back to decade-old theories. The cubic +octet design was chosen for its simplicity, which made it the most straightforward to synthesize with our two-photon lithography and pyrolysis approach.”
The scientists from the architected materials laboratory of UC Irvine professor Lorenzo Valdevit first fabricated a nanoscale closed-cell carbon plate architecture in the cubic+octet design. Fabrication in the nanoscale (the plates were about 160 nanometers or 1/400th the thickness of a human hair) was the method of choice because it avoids the kind of mechanical defects that come with material in larger scales, allowing the researchers to create perfect crystals.
“Materials generally have a characteristic defect size,” Berger explained. “If you can make it really small, then the characteristic defect size is bigger than your structure.”
Creating the tiny cells into a lattice was in itself a win — no one had ever done it with a closed-cell plate architecture. The dominant nanoarchitecture for the last two decades or so, according to the study, have been the more open cylindrical beam “truss” systems. And, while theory had suggested that closed-cell plate designs would be of superior strength, the inability to fabricate them was a major obstacle to proving that — until now.
Perhaps just as satisfying was the next phase of the experiment — crushing the nanolattices. The researchers at UC Irvine compressed carbon plate-nanolattices of varying densities to see what kind of stress and strain they could withstand before failing.
The result? Nanoscale carbon-plate Isomax™ does indeed achieve the upper theoretical bounds of stiffness for its density. The strength of the carbon plate structures was up to 639% stronger and up to 522% stiffer than same-weight beam nanolattices of the same material. “This is the first experimental evidence that plate-architecture is superior to the established beam-architecture,” Bauer said.
“The strength-to-weight ratio of the carbon plate-nanolattices surpasses that of some types of bulk diamond, which is the bulk material with the highest known strength-to-weight ratio,” Valdevit added, crediting the combination of base material and optimal plate-architecture. “There is no other cellular material that has ever achieved that.”
The results offer incontrovertible proof that plate-lattices like Isomax™ are materials of the future.
“What excites me is that this is some of the first evidence, really good evidence,” said Berger, whose metamaterial system is currently being investigated by NASA. “We have world-class processing experts and experimentalists who have made and tested our structural designs, and then shown that they are essentially as good as you can possibly have.” The preeminent metamaterial system — an octet truss lattice designed by Buckminster Fuller — has for decades been the structural design of choice for the space agency, but given the proven superior performance of the cubic + octet closed-cell plate system, NASA is taking an even closer look at Isomax™.
“I stand on the shoulders of more than 40 years of people designing lattices,” Berger said. “So it feels really cool to participate in that lineage.”
Other co-authors on the study included UC Irvine graduate students Cameron Crook and Anna Guell Izard, and researchers from the Martin Luther University, Halle-Wittenberg, Germany. The project was funded by the Office of Naval Research and the German Research Foundation.