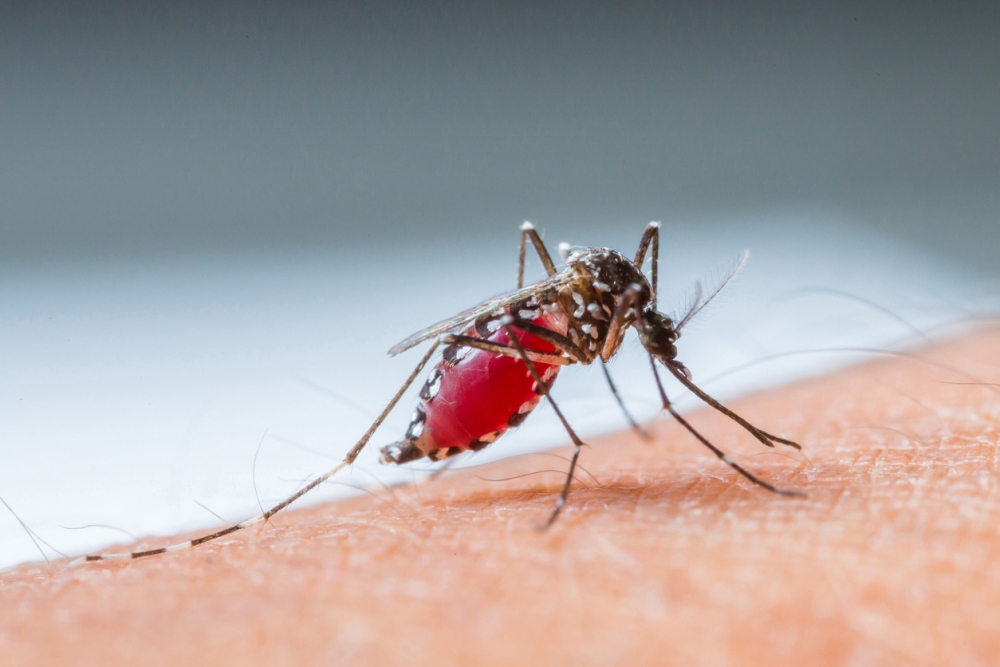
Fighting Malaria, Sustainably
Even as the world’s attentions are currently focused on eliminating COVID-19, there are other diseases that have long been the target of major public health efforts . Among them: malaria — a mosquito-borne parasitic infection that claims almost half a million lives each year, the vast majority of which are in sub-Saharan Africa. Billions of dollars are spent annually on both prevention and treatment, in hopes of eliminating the disease in heavily burdened countries.
But several obstacles persist, not the least of which is the sustainability of manufacturing effective antimalarial drugs. Key questions remain about how they are made, and their cost, especially if they are to be broadly circulated among developing countries.
“Current ways of making these molecules, quite frankly, are traditional. Worldwide, we chemists are utilizing raw materials at an alarmingly unsustainable rate,” said UC Santa Barbara organic chemistry professor Bruce Lipshutz. The petroleum reserves and precious metals such as palladium that are necessary for the preparation of these and many other drugs are in finite supply, he added. Moreover, their extraction is often damaging to the environment, and the chemistry for which they are used is incredibly waste-generating, which necessitates costly handling and cleanup.
There are better, far more benign ways of getting to these molecules, said Lipshutz, who specializes in environmentally responsible synthetic organic chemistry. And now, with a $300,000 grant from the Bill & Melinda Gates Foundation, he is eager to develop these green processes to use in the fight against malaria.
“We’re in a very exciting time here,” Lipshutz said. “I think we can ultimately make these drugs in ways that are both economically attractive and respectful of the environment.”
“I congratulate Bruce Lipshutz on receiving this impressive grant from the Gates Foundation,” said Pierre Wiltzius, dean of mathematical, life and physical sciences at UC Santa Barbara. “As a pioneer in green chemistry, he is uniquely qualified to take on the challenge of revolutionizing pharmaceutical production processes. I applaud his commitment to making crucial life-saving medicines both effective and sustainable.”
Better Chemistry
The project will draw on Lipshutz’s years of experience making modern organic chemistry “green,” that is, cleaner, less wasteful and more eco-friendly.
“We look at three important parameters that everyone in the lab doing organic chemistry has to deal with today,” he said. “When you’re running your reactions, you have to ask, ‘What’s my solvent?’, ‘What conditions do I need to run this reaction?’, and ‘What’s my catalyst?’”
The answers to those questions will indicate potential levels of waste, energy invested and how much of a precious transition metal is required — all areas that can be dramatically improved in the pursuit of chemistry that is as effective as traditional organic synthesis but is, at the same time, a lot gentler on the Earth.
In his work, Lipshutz and his team have developed an enabling technology that allows for metal-catalyzed reactions to be run in water and at room temperature, leaving those waste-generating organic solvents behind, and preferably, in the ground. And what about those precious metals? That know-how is already here, too, and uses 10-100 times less palladium than traditional approaches for the same reactions — thereby extending supplies of endangered metals.
According to Lipshutz, “everything gets recycled — the metals, the water and the technology therein that makes it all possible.” Green drug synthesis, as with pharmaceuticals in general, will require this new way of thinking; a combination of strategies such as these and maybe the reimagining or combining of other processes — for example, methods based on enzymes that also use nature’s solvent: water.
“You just have to plan it out,” Lipshutz said. “You have to do the work to make sure reactions are efficient. You have to know how much of each reagent to put in for the next step, and then the next step, all done in one pot. It’s not a trivial exercise by any means, but it’s absolutely doable.”
Less waste, more efficient use of precious and endangered metals, and streamlined processes also lead to lower manufacturing costs and the ability to keep the price of antimalarials low, especially in the poor countries that need them the most.
“When a company makes a drug and they turn the original synthesis into a greener process, it is always more economically attractive than what they started with,” Lipshutz said. In other words, it’s always a win-win situation. Green always wins.”