The Geometry of Strength
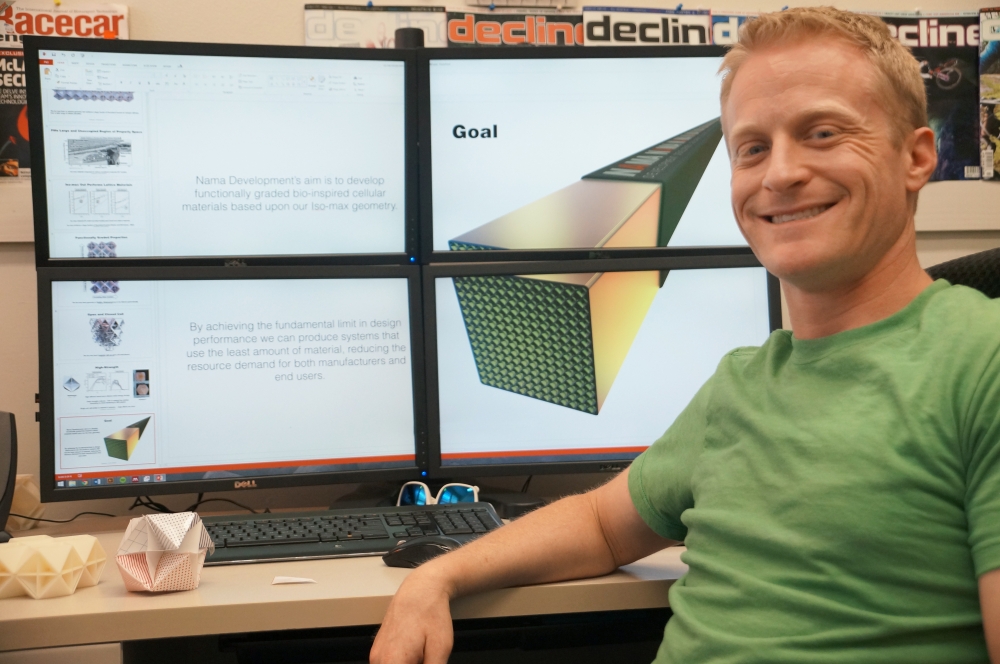
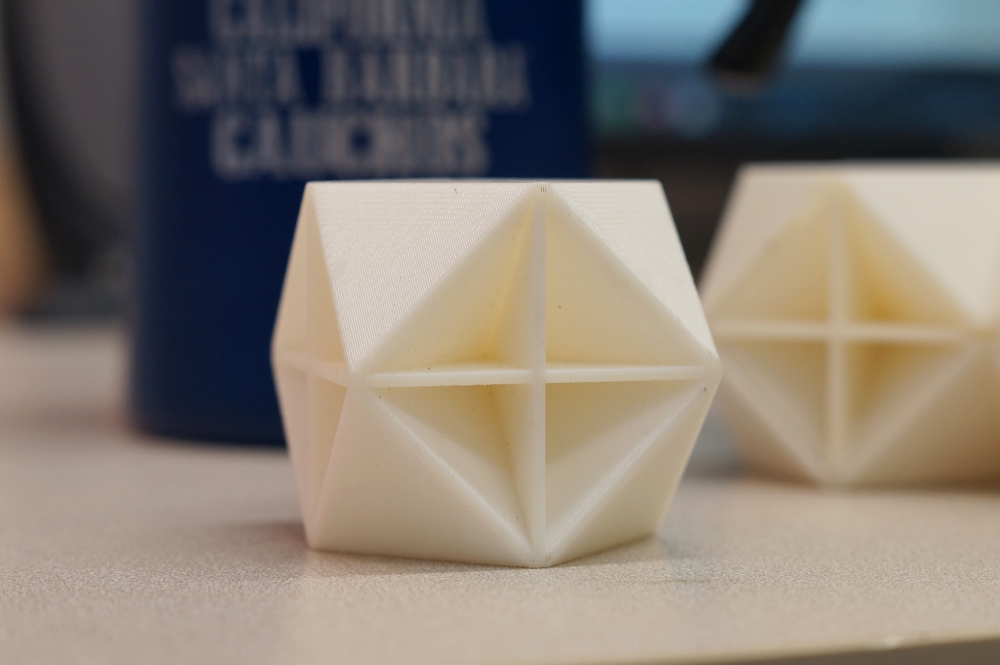
In the world of performance materials, we can be pretty demanding. We want things to be strong but light, flexible but resilient, high quality but easily manufactured and sustainable. UC Santa Barbara mechanical engineer and materials scientist Jonathan Berger has developed a material that can fulfill all those ideals — a solid foam that he describes as “the most efficient in the Universe.”
Called Isomax, this material could also be easily manufactured and, with fairly minor tweaks, changed to emphasize different properties to function in various ways without sacrificing its structural integrity.
According to Berger, the Isomax foam, in comparison to other similar engineering materials, has the highest stiffness to lightness ratio, meaning that for its relatively low density, it has the highest stiffness, resisting crushing and shearing forces that would buckle and flatten denser, heavier materials.
“We were trying to answer the fundamental question of how to add space to stuff,” Berger said, of the research behind Isomax. Void space, he explained, is an aspect that plays an important role in the qualities of virtually every object, such as the functionality of buildings, the taste and texture of foods, or the ability of our shoes to cushion our feet. How that space is utilized, enclosed or set apart, contributes to the objects’ characteristics such as softness, weight, flexibility, stiffness and strength.
Key to the innovative technology behind Isomax is an old science: geometry. The foam has an ordered topology of regularly occurring cells featuring two basic shapes — the triangle and the cross. Taken into three-dimensional space, the cells look like contiguous pyramids — some with three diagonal faces and a base; or four diagonal faces reinforced with diagonal intersecting “walls” in their interiors that resemble the insides of wine cases.
Each shape, said Berger, was chosen because of its unique properties. The intersecting walls of the three-dimensional cross shape are ideal for resisting perpendicular crushing forces, while the pyramidal shapes, long known for their stability, resist shearing forces. Combined in a repeating pattern, these cells are made to withstand forces from all directions while maintaining the foam’s low density, making it ideal as a structural material.
“Because it has certain symmetries and alignments and achieves the theoretical bounds for stiffness, there is no other material like it,” said Berger.
The relatively simple yet effective design lends itself well towards the foam’s creation from a variety of material classes to take advantage of certain properties. The strength and malleability of metals can be used to build futuristic buildings and other structures without sacrificing architectural soundness. Fiber composites in this design could lead to lighter vehicles that are still able to resist the forces of an impact.
Additionally, this solid foam’s versatility can be used as a functionally graded material, useful in situations in which one part of an object must have different physical properties than another part. For instance, a hip replacement must be stiff enough to provide shape and support, while the surface that comes in contact with the pelvis would ideally be soft and flexible enough to allow for weight bearing without grinding away at the socket.
“We can make the walls of the cells thicker and denser at one end and then thinner at the other end,” Berger said. The walls could be removed to leave a lattice structure that could serve as a replacement for knees or other bones that have to provide structure while allowing for blood flow, he added.
Isomax’s low density for its stiffness means that things made from it require less material for the desired amount of strength, added Berger. Using the material in certain objects, such as vehicles, could make them more energy efficient, and the foam’s regularly repeating cellular structure makes it simple to manufacture and scale to demand.
“Jonathan’s achievement opens up opportunities to make structures that engineers will be able to exploit to improve things like implants, sandwich panels for structural stiffness and strength, and multifunctional devices like heat sinks that can also be stiff and strong,” said Robert McMeeking, UCSB professor of materials and of mechanical engineering and one of Berger’s mentors. “His invention is also timely as new fabrication techniques such as 3-dimensional printing now make it possible to manufacture novel geometries such as the one that he has invented.”
Isomax is in the early stages of development, but Berger continues to refine it and prepare it for the market through Nama Development, a company he formed with the help of UCSB’s Technology Management Program.
“There’s been a tremendous amount of support from all over campus,” he said.